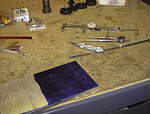 |
After listening to Tony Buchignani tell me about how cool the wheels were on Wedge of Doom, I decided to try them out for myself. But I wanted to really run some torque through them so I machined up some aluminum hubs to clamp the closed-cell foam of the wheel.
To the right I'm employing a quick trick on using a mill to rough out a circle. Simply fix the vertical height of the cutter, make a pass, then rotate the part on some axle. It lets you get really close in a few minutes with a minimum of setup changes. |
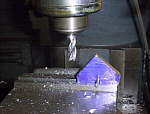 |
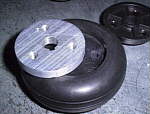 | The new Al hub was tapped in three places to permit the older plastic version to be clamped through with some 1/4-20 cap screws. By squeezing the core of the tire I was going to transmit torque to the tread. You can't drill through this foam without it ripping apart. So I heated up a chunk of key stock in the torch and burned clearance holes for the cap screws. I never turn down a chance to work with fire. |
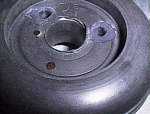 |
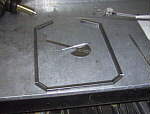 |
I originally planned for the 25 kg class so a square tube steel frame was the only way to go. I figured it should have some sort of cool shape, other than a box. So I used the classic 45 vs. 60 degree angle approach. |
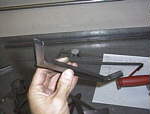 |
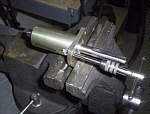 |
I really scored on the wheel mounts - surplus aerospace stuff from the Surplus Center catalog. A stainless steel shaft with pressed-on ball bearings all in a flanged aluminum housing for $7. Here I am tapping the mounting holes for attachment to the frame. | 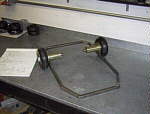 |