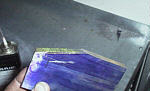 |
This hacksaw cut took almost 30 minutes. That's becuase the blued chunk of steel I'm holding is coded "O1," a high carbon grade that has already been oil hardened. It's a bit different to work with, most changes involving lots of coolant and decreased cutting speeds. But its toughness makes it an excellent choice for the Ax's prong bumpers, seen below. |
 |
Here is the second bumper on the mill bed, getting its finishing cut. As I mentioned above, the Ax hits 20 MPH at full stick. This makes ramming an attractive attack mode, as opposed to shoving, which the Agamemnon was good at last year. The new "no pinning" rule also favors speed above power, not to mention that fast robots crashing into each other is what the audience is paying big bucks to watch. |
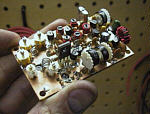 |
Three late night sessions in the electronics design wing converted a bag of parts into a 900 MHz transmitter, the source of the Ax's reverse video link. And yup, I wound those little red coils myself. The camera, bagged from the dormant Ag, is slated to be mounted on the forearm of the Edger to allow Weapons Officer Dave to see what he's slicing into. We'll certainly provide an audience feed this year in case anyone wants to write the video to tape. |
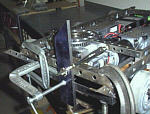 |
Ah yes, another famous "using all the clamps in the shop" picture. I really should by stock in ViseGrip. Here I've got the bottom support of the front structural frame jigged up so I can weld it all together. The chunks of 1018 flat stock serve as large alignment tools when not being cut and machined themselves, a useful property of their ground surface dimensions. |
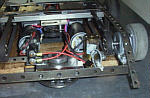 |
Here the Ax is flipped on its back, revealing some of its internals. Starting in the upper part of the picture, the two black cylinders with silver caps are the drive motors. Note the vents on the end facing you, where the cooling flow exits. Left foreground is the high current solenoid that switches the 25v into the Edger's cutter motor. Center is the shaft clamp that keeps the whole turntable bearing system intact. To the right is the Pittman motor that spins the turntable. |
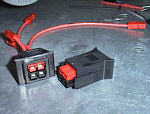 |
One of the oft-overlooked rules of the event is to provide an easily accessable on/off switch for the robot. Here is my safety interlock that disconnects the battery power from the speed controllers with a quick yank. The motors I've used draw 80A at full stall, meaning that the 30A lighted toggle switches I used last year weren't an option. I wanted something really solid with low line losses, and safety-judge-approved. In fact, I've used these Anderson connectors with 12ga silicone wire throughout the high current circuits in the Ax. |
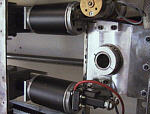 |
You're looking at a unique spot on the Ax - unused space. In the design I managed to leave a few small gaps open for any last minute battery or connector requirements.
|
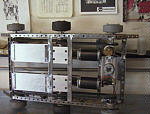 |
Here I have the entire driveline completed and attached. As you can see, the middle wheel on each side is wider than the fore and aft units. This is what happens when the December "Torque was king last year" brain doesn't communicate clearly with the March "Torque is out, speed is in" brain. I could spin out the wheels on the Ag last year, so I didn't want that to happen this year, thus the wide center tires. But since the Ax doesn't present the same amount of torque to the wheels, I'll be switching back to thin tires in the middle, saving over a pound of weight in the process.
|
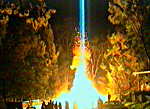 |
After you're through with this status report, and if you liked Daniel's Volvo quote, jump over to his web page for some interesting content. Your horizons will be expanded.
|